Appendix E to Part 157 - Specifications for the Design, Installation and Operation of a Part Flow System for Control of Overboard Discharges
33:2.0.1.5.26.11.195.1.12 : Appendix E
Appendix E to Part 157 - Specifications for the Design,
Installation and Operation of a Part Flow System for Control of
Overboard Discharges
Source. Appendix 2 to Annex 5 of IMO's Marine Environment
Protection Committee document MEPC/Circ. 97. Paragraphs 1 and 2 are
printed for information. Paragraphs 3, 4, and 5 are incorporated
into §§ 157.11 and 157.37.
Note:
Information in square brackets on Figure 1 has been added by the
Coast Guard for clarity.
1
Purpose
The purpose of these Specifications is to provide specific
design criteria and installation and operational requirements for
the part flow system referred to in Regulation 18(6)(e) of Annex I
of the International Convention for the Prevention of Pollution
from Ships, 1973 as modified by the Protocol of 1978 relating
thereto.
2
Application
2.1 Existing oil tankers may, in accordance with Regulation
18(6)(e) of Annex I of MARPOL 73/78, discharge dirty ballast water
and oil contaminated water from cargo tank areas below the
waterline, provided part of the flow is led through permanent
piping to a readily accessible location on the upper deck or above
where it may be visually observed during the discharge operation
and provided that the arrangements comply with the requirements
established by the Administration and which shall at least contain
all the provisions of these Specifications.
2.2 The part flow concept is based on the principle that the
observation of a representative part flow of the overboard effluent
is equivalent to observing the entire effluent stream. These
specifications provide the details of the design installation, and
operation of a part flow system.
3
General Provisions
3.1 The part flow system shall be so fitted that it can
effectively provide a representative sample of the overboard
effluent for visual display under all normal operating
conditions.
3.2 The part flow system is in many respects similar to the
sampling system for an oil discharge monitoring and control system
but shall have pumping and piping arrangements separate from such a
system, or combined equivalent arrangements acceptable to the
Administration.
3.3 The display of the part flow shall be arranged in a
sheltered and readily accessible location on the upper deck or
above, approved by the Administration (e.g. the entrance to the
pump room). Regard should be given to effective communication
between the location of the part flow display and the discharge
control position.
3.4 Samples shall be taken from relevant sections of the
overboard discharge piping and be passed to the display arrangement
through a permanent piping system.
3.5 The part flow system shall include the following
components:
.1 Sampling probes;
.2 Sample water piping system;
.3 Sample feed pump(s);
.4 Display arrangement;
.5 Sample discharge arrangement; and, subject to the diameter of
the sample piping:
.6 Flushing arrangement.
.3.6 The part flow system shall comply with the applicable
safety requirements.
4
System Arrangement
4.1 Sampling points.
4.1.1 Sampling point locations:
.1 Sampling points shall be so located that relevant samples can
be obtained of the effluent being discharged through outlets below
the waterline which are being used for operational discharges.
.2 Sampling points shall as far as practicable be located in
pipe sections where a turbulent flow is normally encountered.
.3 Sampling points shall as far as practicable be arranged in
accessible locations in vertical sections of the discharge
piping.
4.1.2 Sampling probes:
.1 Sampling probes shall be arranged to protrude into the pipe a
distance of about one fourth of the pipe diameter.
.2 Sampling probes shall be arranged for easy withdrawal for
cleaning.
.3 The part flow system shall have a stop valve fitted adjacent
to each probe, except that were the probe is mounted in a cargo
line, two stop valves shall be fitted in series, in the sample
line.
.4 Sampling probes should be of corrosion resistant and oil
resistant material, of adequate strength, properly jointed and
supported.
.5 Sampling probes shall have a shape that is not prone to
becoming clogged by particle contaminants and should not generate
high hydrodynamic pressures at the sampling probe tip. Figure 1 is
an example of one suitable shape of a sampling probe.
.6 Sampling probes shall have the same nominal bore as the
sample piping.
4.2 Sample piping:
.1 The sample piping shall be arranged as straight as possible
between the sampling points and the display arrangement. Sharp
bends and pockets where settled oil or sediment may accumulate
should be avoided.
.2 The sample piping shall be so arranged that sample water is
conveyed to the display arrangement within 20 seconds. The flow
velocity in the piping should not be less than 2 metres per
second.
.3 The diameter of the piping shall not be less than 40
millimetres if no fixed flushing arrangement is provided and shall
not be less than 25 millimetres if a pressurized flushing
arrangement as detailed in paragraph 4.4 is installed.
.4 The sample piping should be of corrosion-resistant and
oil-resistant material, of adequate strength, properly jointed and
supported.
.5 Where several sampling points are installed the piping shall
be connected to a valve chest at the suction side of the sample
feed pump.
4.3 Sample feed pump:
.1 The sample feed pump capacity shall be suitable to allow the
flow rate of the sample water to comply with 4.2.2.
4.4 Flushing arrangement:
.1 If the diameter of sample piping is less than 40 millimetres,
a fixed connexion from a pressurized sea or fresh water piping
system shall be installed to enable flushing of the sample piping
system.
4.5 Display arrangement:
.1 The display arrangement shall consist of a display chamber
provided with a sight glass. The chamber should be of a size that
will allow a free fall stream of the sample water to be clearly
visible over a length of at least 200 millimetres. The
Administration may approve equivalent arrangements.
.2 The display arrangement shall incorporate valves and piping
in order to allow a part of the sample water to bypass the display
chamber to obtain a laminar flow for display in the chamber.
.3 The display arrangement shall be designed to be easily opened
and cleaned.
.4 The internal of the display chamber shall be white except for
the background wall which shall be so coloured in order to
facilitate the observation of any change in the quality of the
sample water.
.5 The lower part of the display chamber shall be shaped as a
funnel for collection of the sample water.
.6 A test cock for taking a grab sample shall be provided in
order that a sample of the water can be examined independent of
that in the chamber.
.7 The display arrangement shall be adequately lighted to
facilitate visual observation of the sample water.
4.6 Sample discharge arrangement:
.1 The sample water leaving the display chamber shall be routed
to the sea or to a slop tank through piping of adequate
diameter.
5
Operation
5.1 When a discharge of dirty ballast water or other oil
contaminated water from the cargo tank area is taking place through
an outlet below the waterline, the part flow system shall provide
sample water from the relevant discharge outlet at all times.
5.2 The sample water should be observed particularly during
those phases of the discharge operation when the greatest
possibility of oil contamination occurs. The discharge shall be
stopped whenever any traces of oil are visible in the flow and when
the oil content meter reading indicates oil content exceeds
permissible limits.
5.3 On those systems that are fitted with flushing arrangements,
the sample piping should be flushed after contamination has been
observed and additionally it is recommended that the sample piping
be flushed after each period of usage.
5.4 The ship's cargo and ballast handling manuals and, where
applicable, those manuals required for crude oil washing systems or
dedicated clean ballast tanks operation shall clearly describe the
use of the part flow system in conjunction with the ballast
discharge and the slop tank decanting procedures.
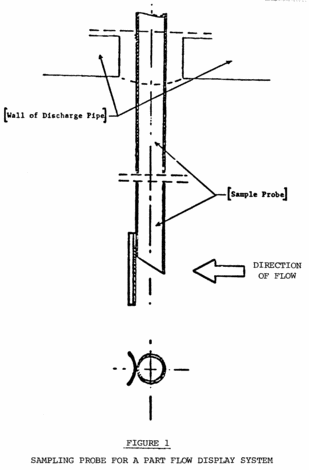
[CGD
75-124a, 48 FR 45721, Oct. 6, 1983]